The WeldMagnet from WeldNova
Unleash the full potential of high-performance welding processes
Contactless
The magnetic weld pool backing system works without a fixed connection to the workpiece. No assembly is required and you can switch flexibly between components.
Powerful
The system works across a wide performance spectrum, allowing you to cover large tolerances in gap dimensions or a wide variation in sheet thicknesses.
Universal
The system is not process- or material-dependent. For example, you can easily switch between steel and aluminum. Other materials are also possible. Just get in touch with us!
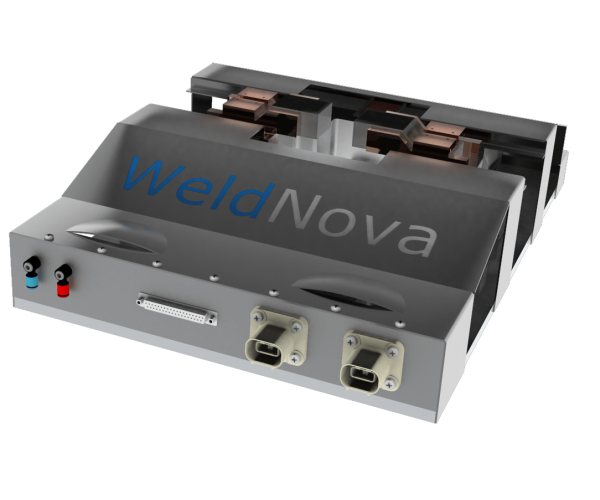
The WeldMagnet from WeldNova
Welding thick-walled components in the 1G position is difficult due to the increased hydrostatic pressure and the resulting droplet formation on the root side. If the surface tension can no longer compensate for the hydrostatic pressure, the molten metal will drip out. To prevent this, a melt pool support is often used. However, conventional bath supports made of ceramic, for example, require time-consuming mechanical removal.
The innovative contactless magnetic weld pool backing counteracts gravity-induced dripping of the melt and compensates for hydrostatic pressure, opening up completely new possibilities when using high-performance welding processes. The effective range of the magnetic field is large, so that even low positioning accuracies do not restrict the result of the weld seam.
Application of the WeldMagnet
The contactless magnetic weld pool backing works regardless of which welding process is used. The interaction between the magnetic field and the dripping melt is crucial for influencing and controlling the droplet formation.
Below the welding zone, eddy currents are induced by a magnetic field, which counteract the hydrostatic pressure of the molten metal and enable a reliable welding process without droplet formation. In this way, very thick sheets can be welded in a single layer with excellent quality. For example, when welding high-strength, thermomechanically rolled steels, a slow welding speed can be set to specifically reduce the cooling rate. This promotes the mechanical-technological properties, in particular the notched impact strength, and helps to prevent cracks.
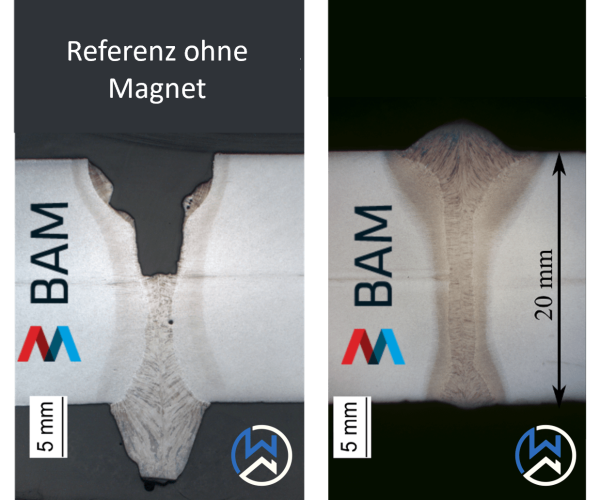
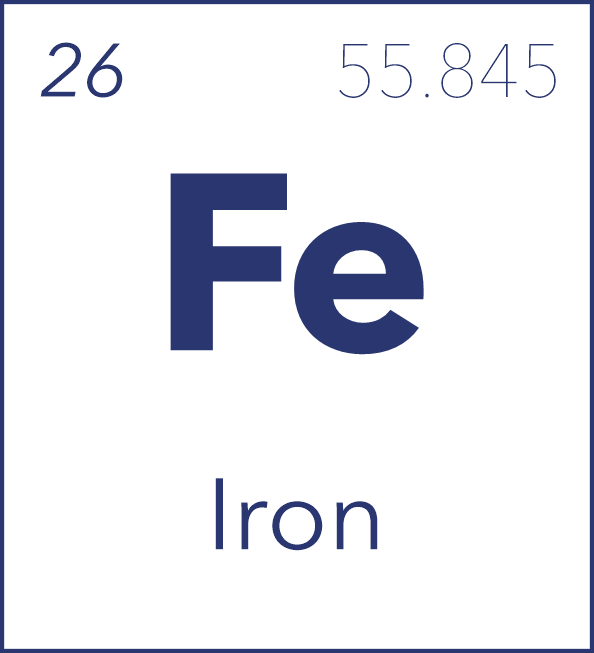
SteeL
All steel materials and alloys, in particular steel grades for the wind industry and shipbuilding

Aluminium
All aluminium materials and alloys
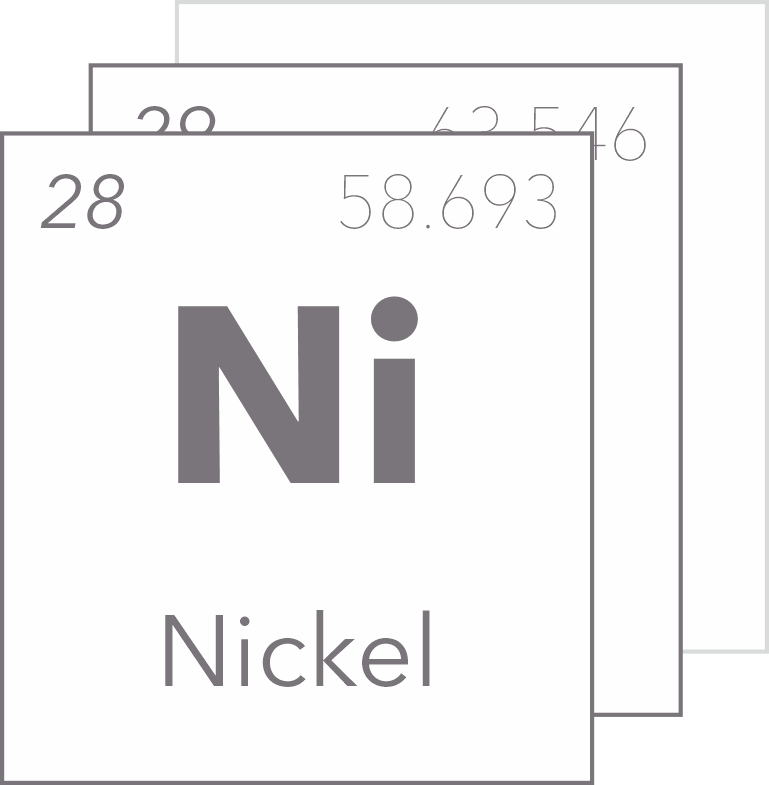
many More
Further materials on request
The magnet is not limited to welding steel and can be used for many materials
Mechanical properties can be matched to the application
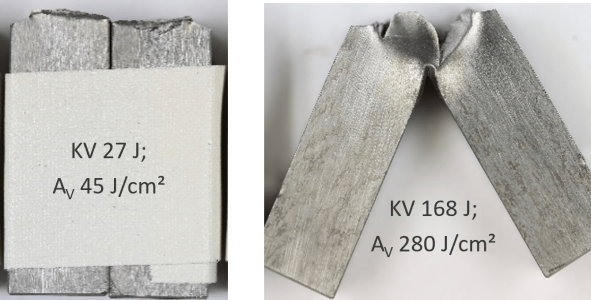
The properties of the molten pool can be modeled with the magnet system. By adjusting the cooling rates, for example, the mechanical properties of the seams can be adjusted almost at will.
Save costs and produce more? Let us support you!
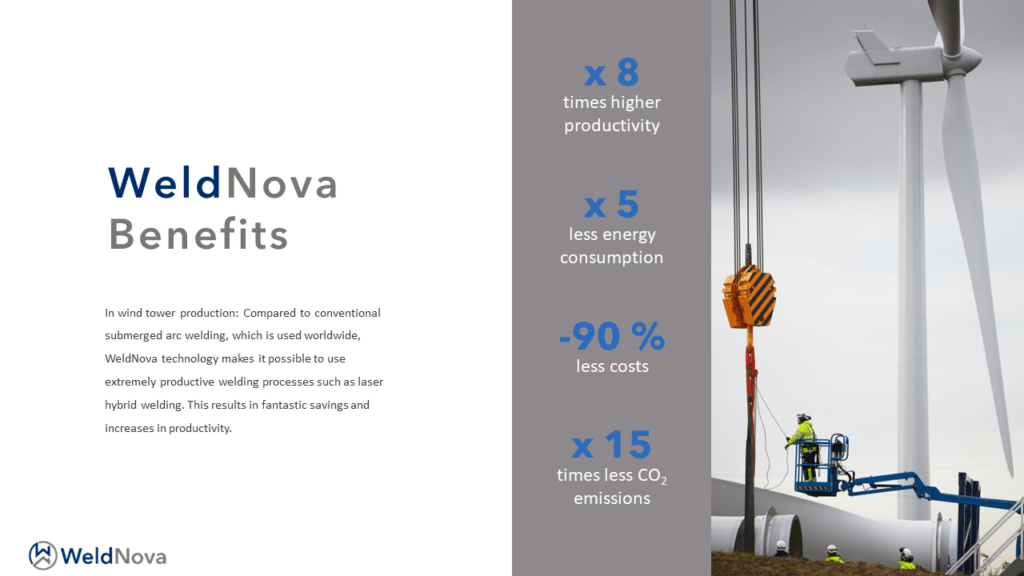
An example from the Wind industry
Wind towers are currently joined using the submerged arc welding process. Many layers are required to be able to join the component thicknesses of 25 mm. This not only leads to very high material consumption (filler material, powder), but also to high energy input. Overall, wind towers are manufactured at a very high cost in terms of time and money.
Laser beam hybrid welding with the use of a contactless magnetic weld pool backing, on the other hand, allows the welding of 25 mm thick components in just a single layer. In addition, a higher welding speed can be achieved, resulting in enormous time savings. This not only saves on material consumption, but also significantly reduces CO2 emissions. You can save time not only in the welding process; seam preparation is no longer necessary. Even components that have been prepared with a flame cut can be joined without any problems.
Read more about our case study!
The advantages of the WeldNova magnet system
The WeldNova magnet system offers a number of advantages for your welding process. Depending on the application, different aspects are in the foreground and are pronounced to varying degrees. We would be happy to calculate the exact advantages for your application without obligation.
Please contact us.
- Contactless in relation to the workpiece and the process zone. No mounting or dismounting on the workpiece is required.
- No consumables required. Low machine wear.
- Suitable for continuous production.
- Can be combined with almost all common machine-guided welding processes.
- No need for edge preparation such as milling.
- Precise adjustment of heat conduction in the component. This makes it possible to define temperature gradients.
- Pores in the weld seam can be significantly reduced.
- The mixing of the filler material can be significantly improved over the entire seam cross-section.
- The gap bridging capability is significantly increased.
- The tolerance for the edge offset can be extended considerably.
- 1-2 layer welding of sheets with a thickness of up to 40 mm possible.
Download free case study in wind tower construction

Increase the efficiency of your existing production line with a retrofit from WeldNova
By retrofitting existing systems, you can increase the productivity of your manufacturing by several times with our technology. Get in touch for advice!