The revolution in thick plate welding: Discover the electromagnetic weld pool backing
A contactless electromagnetic backing has considerable advantages.
Reduce your costs and increase your productivity.
Find out what we can do for you!
Learn more about contactless electromagnetic weld pool backing
The WeldNova GmbH has many years of experience in the welding of thick sheets. We specialize in the use of non-contact electromagnetic weld pool backing for a wide variety of welding processes. Whether laser beam welding, arc welding or laser beam-arc hybrid welding; our flexible system can be used for all these applications. In particular, the number of layers can be reduced and material consumption lowered. We can also help you to integrate our technology into your existing system technology and bring your production chain up to the latest state of the art.
The field of application is not limited to thick sheets. The use of magnetic fields also brings considerable advantages for thin sheet applications, such as improving porosity, surface roughness or optimizing the upper bead geometry. We would be happy to assist you!
Advantages of the technology
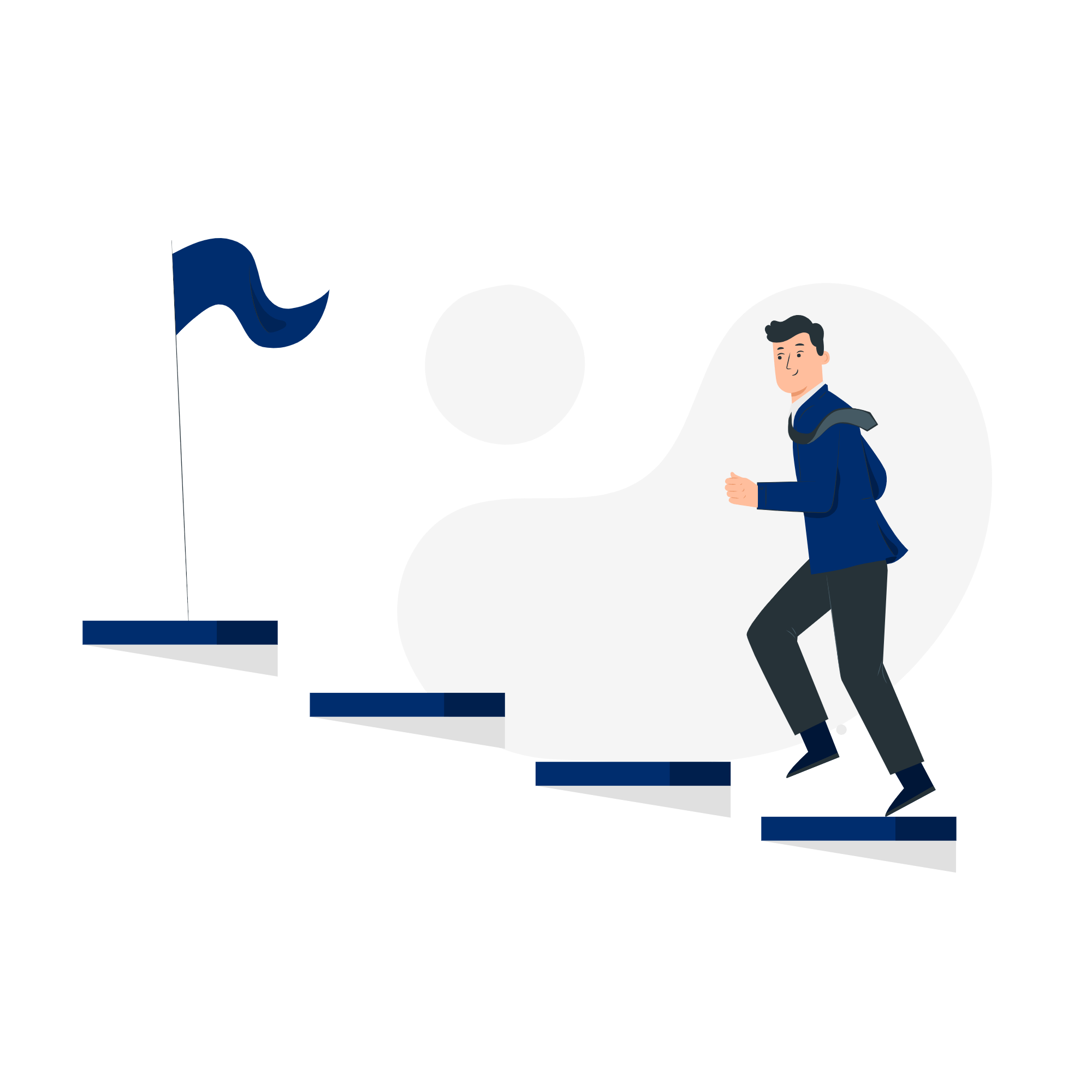
Increase of Productivity
The use of electromagnetic backing increases the welding speed. This boosts the productivity of a welding station and allows more products to be produced in less time.
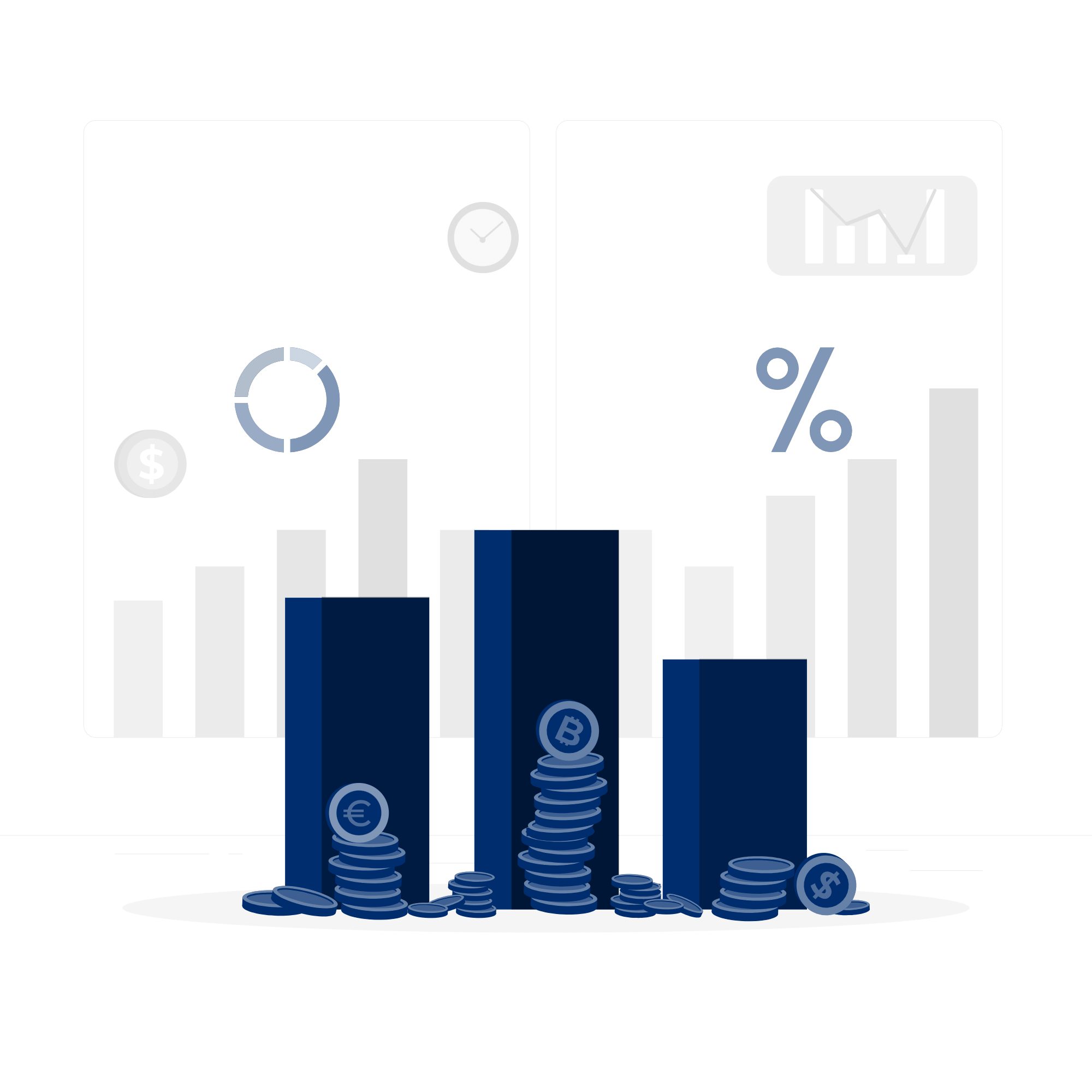
Less Costs
Significant savings in energy, consumables, waste and filler materials can be achieved. Learn how you can drastically reduce production costs.
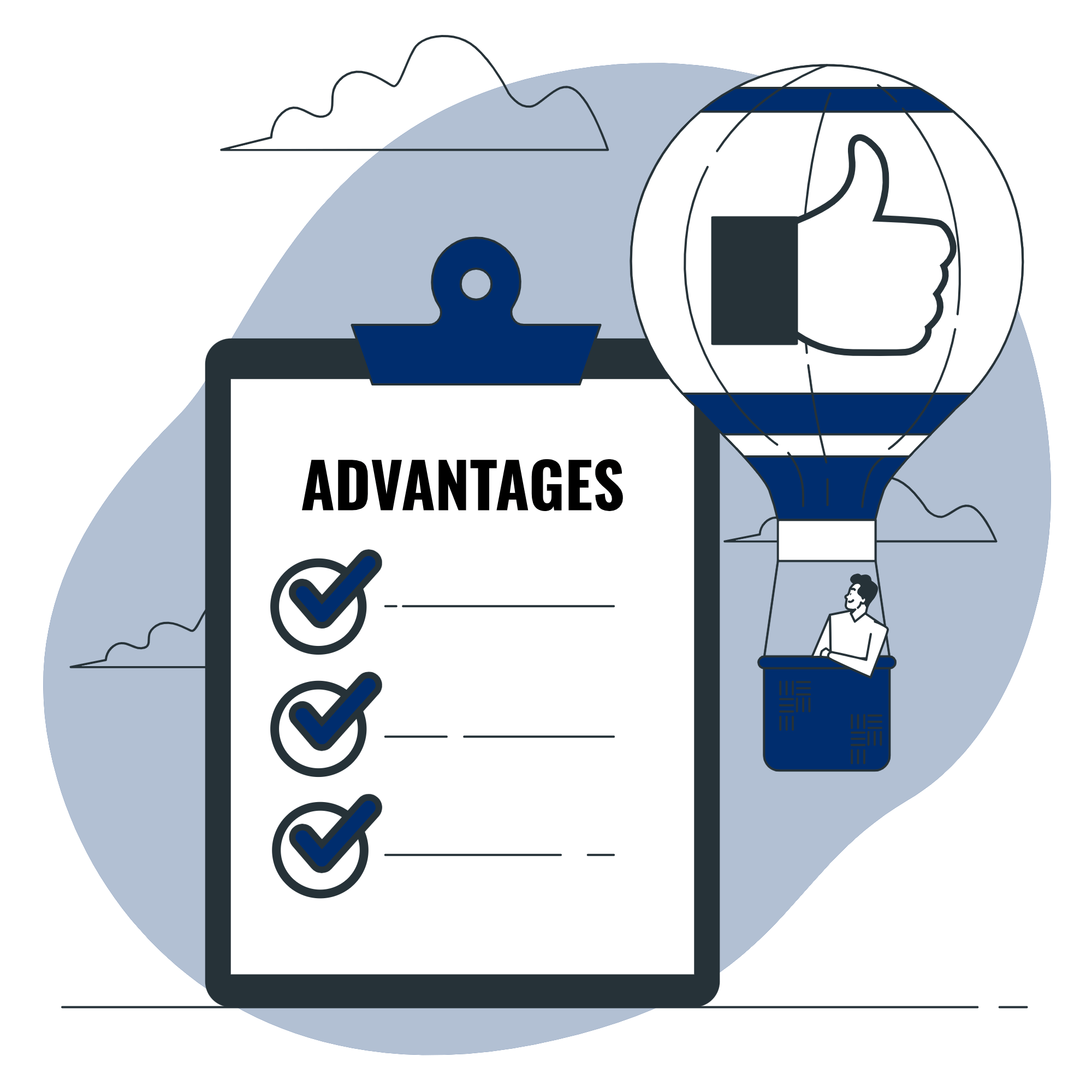
Competitive advantage
Electromagnetic backing can be easily integrated into existing plant technology. This means you can gain a considerable competitive advantage with low investment costs.
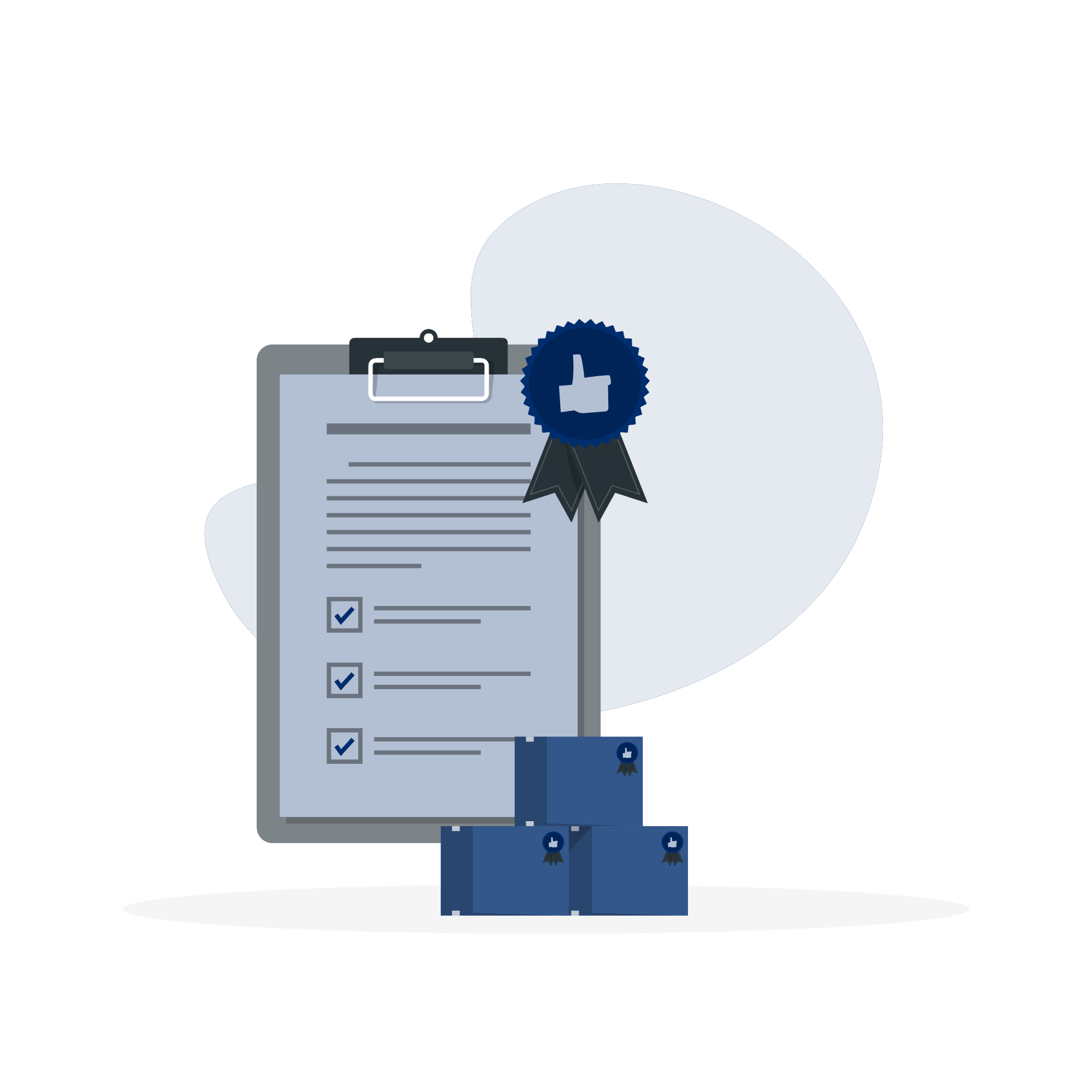
High Quality
Our technology is designed to be extremely robust in order to always deliver the same quality. We guarantee you the highest standard-compliant quality of weld seams with significant increases in productivity.
Areas of application of the WeldNova technology
Our innovative solutions are particularly attractive for welding thick sheet metal. Be it the welding of thick-walled pipes for the wind industry and pipeline construction or ship panels, our technology captures the full potential of high-performance welding processes.
Also thin-walled components such as those used in the automotive industry can be welded efficiently. We will be happy to inform you about the various possible applications.
Wind industry
Shipbuilding
Pipelinebuilding
Automobile industry
We support you with your welding task
Our services at a glance:
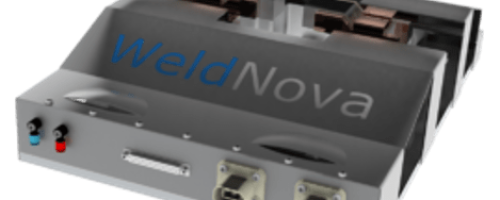
Magnet-Technology
We integrate magnet technology into your new or existing system, regardless of the manufacturer. This means that your production or customer project can also benefit from the advantages of the technology.
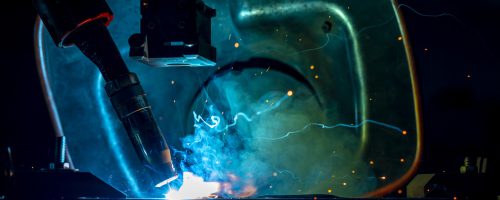
Process Development And
Process optimization
At WeldNova, you are at the center of our mission. We believe that the key to sustainable growth and success lies in the continuous improvement of manufacturing processes.
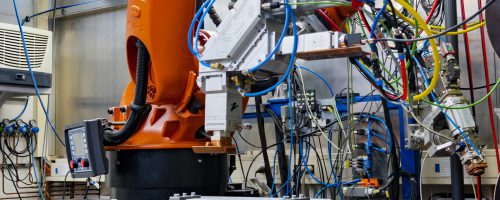
Contract Manufacturing
Contract manufacturing is the cornerstone of our pursuit of excellence. With a heritage of expertise and an unwavering commitment to quality, we offer you our services.
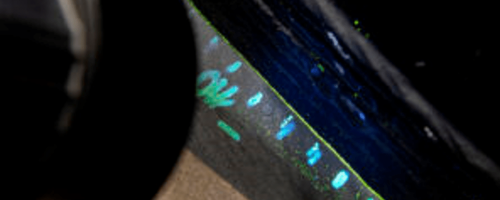
Consulting
Are you interested in our expertise or would you like to use our technology? WeldNova will be happy to advise you on all topics relating to efficient automated welding with arc, laser or laser-arc hybrid processes.
Revolutionize your plant technology
We will be happy to advise you!
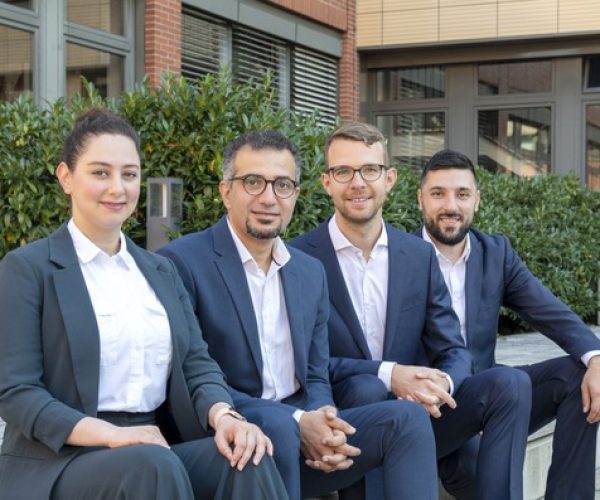
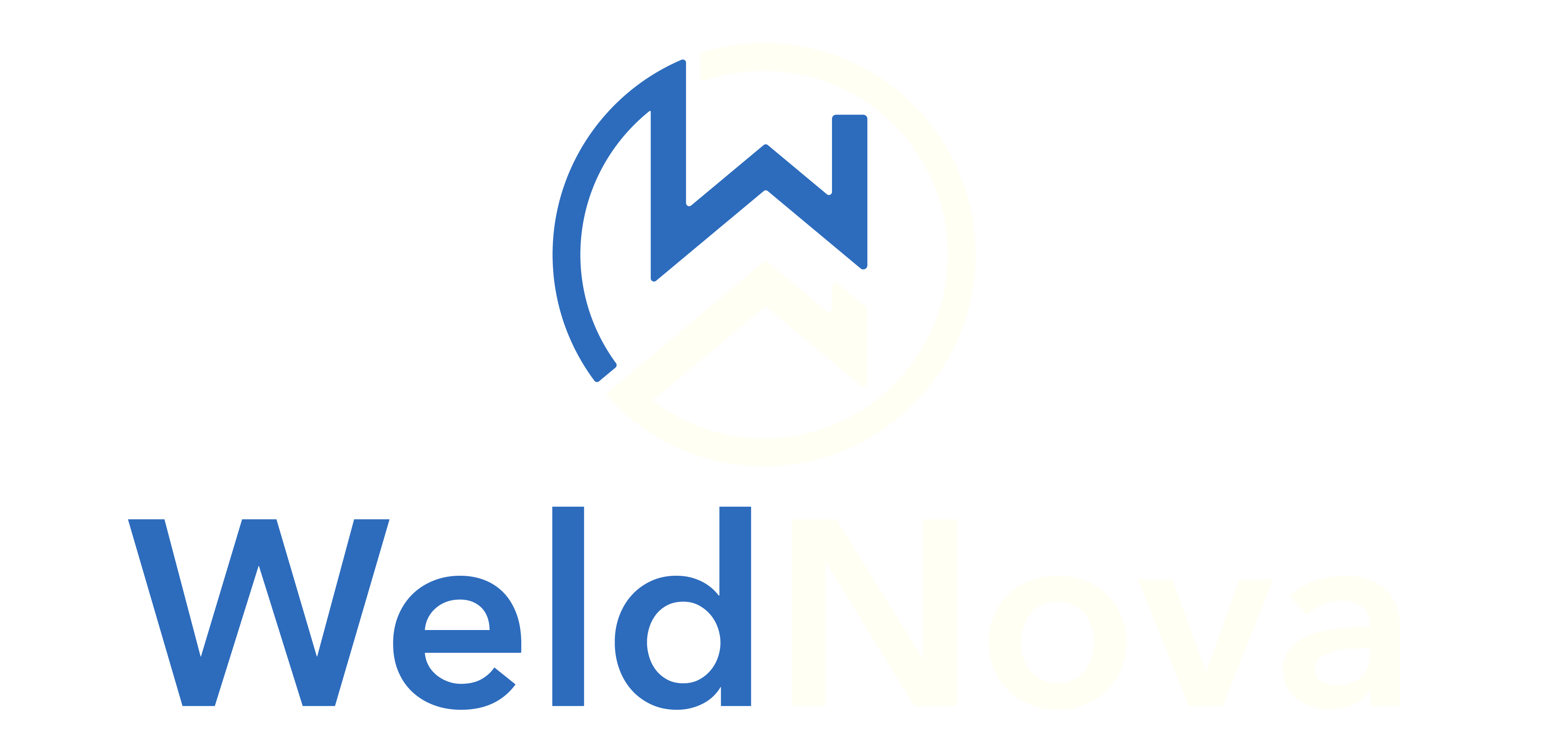
WeldNova combines many decades of experience in applied research and fundamental research in welding technology. The team passionately pours this know-how into innovative welding solutions. The core technology of WeldNova GmbH enables us to push the boundaries of what is possible in the welding industry.
Revolutionize the welding of thick-walled components with our innovative electromagnetic weld pool backing technology. Conventional welding processes such as submerged arc welding require extensive preparation and multiple welding layers, resulting in high costs and very long welding times. Our non-contact electromagnetic technology prevents droplet formation, enabling single-pass welding without the need for time-consuming edge preparation. This leads to significantly higher productivity, considerable cost savings and reduced CO2 emissions. The technology has a wide range of applications, from wind energy and shipbuilding to bridge building and vehicle construction. With the potential to transform industries, our magnet system can be easily integrated into existing and new welding systems.